At present, there is a clear trend of large-scale wind turbine blades, from the previously common 30 to 40 meters to the current 70 to 80 meters. The blade application scenarios are also distributed in high mountains, inland areas, offshore areas, etc. With the development of wind farms in southern mountains and plains, the quality of wind resources has been declining. In fact, there are wind farms with wind speeds below 5m/s in the investment wind farms. After adopting wind turbines with large impeller diameters, the number of hours has also exceeded 2,000 hours and is ready for development. At present, the impeller diameter of the 2.0MW class has exceeded 135m, the impeller diameter of the 2.5MW has exceeded 145m, and the highest of the 3.0MW class has reached 164m, and the blade length exceeds 80m. With the increasing size of blades and the complexity of transportation roads, blade transport vehicles have also been continuously upgraded to adapt to new transportation requirements and formed specific reverse transport vehicles. They pass through villages, mountainous plains and deserts. Compared with semi-trailers, more and more blade transport vehicles are used for blade transportation. At present, the latest reverse transport vehicle is a blade reverse transport vehicle with hydraulic rear wheel steering, lifting and leveling and lifting functions. It has 24 tires and a turning radius of less than 16 meters. The hydraulic steering device can rotate the wind blades 360 degrees and can also achieve a 45-degree lift to flexibly avoid various obstacles encountered on the way. As the blades become longer and longer, this blade lifting vehicle with rear wheel steering, lifting and leveling functions can not only be more suitable for complex terrain, but also reduce the turning radius of the road, thereby significantly reducing the road construction cost of the wind farm, which is conducive to reducing the cost of electricity.
Introduction to several examples of blade transfer vehicles
- The seventh generation blade transfer vehicle is mainly for 121 blade transportation. At present, the maximum capacity is 131, with more counterweights.
- The eighth generation blade transporter adopts a gooseneck structure for the main beam of the tooling. It makes full use of the gooseneck space of the trailer, optimizes the tooling, transports 121, has less counterweight, and the rear axle of the trailer is exposed, which is conducive to reducing the situation where the rear wheel is seriously overloaded when going uphill.
- The ninth generation blade transporter (four-axis) adopts a 3.4-meter four-axis semi-trailer, 8.25R16 tires, and a telescopic hydraulic outrigger at the tail end. The blades are safer to turn around. It has lifting and leveling and rear wheel steering functions, better cornering passability, and a smaller turning radius.
- The tenth generation blade transporter adopts a 15mX3.6m three-line six-axle semi-trailer. The rear wheel has hydraulic outriggers, which makes it safer to turn around the blades. The blade flange uses a 50mm steel plate, which shortens the size. The blade is installed at the back to reduce the counterweight. It mainly transports 140-164 blades, with a smaller turning radius and good cornering passability.
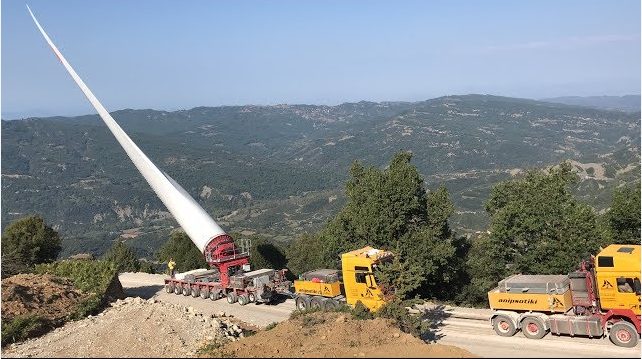