A semi-trailer tanker is a tanker that uses a traction head to connect the trailer part. Compared with ordinary single-type tankers, semi-trailer tanker oil transportation can effectively improve transportation efficiency. Under the same tonnage, it reduces transportation costs and saves fuel consumption. It is mainly composed of a tank body, a frame, a traction device, a support device, an electrical system, a travel system, a protective device, and accessories.
A semi-trailer tanker is divided into two parts, the tank part and the frame or the travel part that supports the tank body. The rear part of the semi-trailer tanker is generally the same, with rear double axles (two axles) and rear triple axles (three axles). The traction head is selected according to needs. Semi-trailer tankers are usually called by the brand of the traction head.
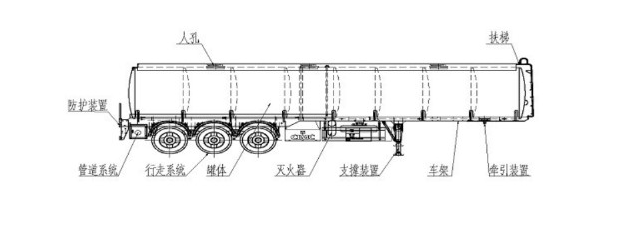
- Tank body of semi-trailer tanker
The tank body is made of 4mm or 6mm high-quality carbon steel produced by the steel company according to national standards. The shape is divided into elliptical or square round tank bodies, which can hold 1-4 kinds of oil products. Heating and insulation series tank bodies can also be produced.
Alcohol and chemical tankers are made of stainless steel imported from South Korea with a thickness of 4mm-5mm.
All kinds of hydrochloric acid, sulfuric acid and alkali liquid tank trucks are made of plastic with a thickness of 12mm-22mm.
Multiple wave-proof baffles are installed in the tank body. High-pressure gas leak detection is used to make the tank body have high strength, stable center of gravity, safe and stable vehicle transportation, etc.
According to the purpose of the tank truck, centrifugal pumps, gear pumps, and stainless steel pumps can be selected, which have the characteristics of large flow and fast suction speed.
The measurement of oil tank trucks can choose single-count and double-count flow meters, and can also be equipped with tax-controlled computer refueling machines, 10-15 meters automatic retractable return reels, and refueling guns. Edible oil products can be measured by edible oil computer meters. - Features of semi-trailer oil tank trucks:
Medium: gasoline, diesel, etc.
Tank material: imported aluminum alloy.
Tank shape: oval, round.
Unloading system: bottom loading system, oil and gas recovery system, anti-overflow system.
Features: light weight, large load capacity, high transportation efficiency and operating income, good conductivity, high safety performance, no rust, no pollution to the shipping medium. - Special configuration of semi-trailer tanker:
The conventional configuration of the previous tanker is a special oil pump, equipped with a pump inlet and outlet pipe. This pipe has two types: Wuhan carbon steel and 304 stainless steel. The refueling or oil transport tank is generally from 5 cubic meters to 30 cubic meters. There are also some semi-trailers with a capacity of 55 cubic meters. The main way of oil intake for tankers in the past was to refuel from the manhole above the tank body. However, in order to improve safety, our tanker production has been made into a bottom canning process, which is the so-called European standard bottom oil filling process.
What is bottom canning? Bottom canning is also called bottom oil filling system. The important components required for bottom filling modification: The main components of bottom canning are exhaust gas recovery system, anti-overflow system, seabed valve, European standard tank mouth, probe, SO2 socket, anti-static system, bottom canning API joint, etc. Our main production process is: steam purging, washing and wiping the tank; cutting the oil collection tank, installing the seabed valve; installing the oil system; installing the gas phase circuit; replacing the closed manhole cover (European standard manhole cover); water pressure, airtightness, kerosene leak test.
This is the overall working picture of the lower oil loading system, from which we can see the importance of the electrostatic grounding belt. This kind of electrostatic grounding device of large gas stations is mainly fixed, which is generally solved by gas stations. They install one near the large landlord oil depot. When each refueling truck comes to refuel, it can be quickly connected. The electrostatic grounding alarm is a standardized anti-static product for oil loading and unloading occasions. It can not only introduce the static electricity generated during the liquid transfer process into the earth, but also automatically detect the grounding condition throughout the process. When the grounding is poor or disconnected, the sound alarm will be sounded to ensure the safety of production operations.
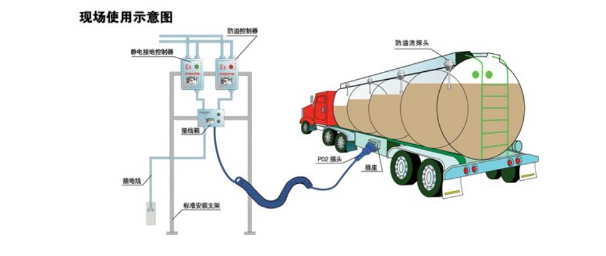