Powder and Particle Material Transport Semi-trailer
Powder and Particle Material Transport Semi-trailer is a special vehicle for transporting large quantities of dust materials (bulk cement). It is generally suitable for areas that strictly implement weight-based charges in accordance with national regulations. The volume is generally between 35-45 cubic meters. It is suitable for the transportation and pneumatic unloading of dry powder materials with a particle diameter of no more than 0.1mm, such as fly ash, cement, lime powder, and ore powder. When the vertical height of unloading reaches 15m, the horizontal conveying distance can reach 5m.
The semi-trailer powder and particle material transport vehicle uses the power of its own engine to drive the on-board air compressor through the power take-off, and sends compressed air through the pipeline into the air chamber at the bottom of the sealed tank body, so that the cement on the fluidized bed is suspended in a fluidized state. When the pressure in the tank reaches the rated value, the unloading butterfly valve is opened, and the fluidized cement flows through the pipeline for transportation. It is made using domestic advanced technology, with novel design, sturdy and durable. The air bag type has a large load capacity, fast unloading speed and small residual volume. The integrated tank body has the characteristics of high overall strength, good rigidity, good pressure bearing and good performance.
The fluidized bed in the tank is scientifically designed and reasonably arranged, which can effectively shorten the unloading time to 1.4T/min, improve the volume utilization rate of the tank body, and reduce the residual ash rate to 0.2%. The tank body of the powder and particle material transport vehicle adopts a double-cone inward-inclined horizontal structure, double-tube air intake and double-tube feeding. Its unloading speed and residual rate meet the requirements of industry standards.
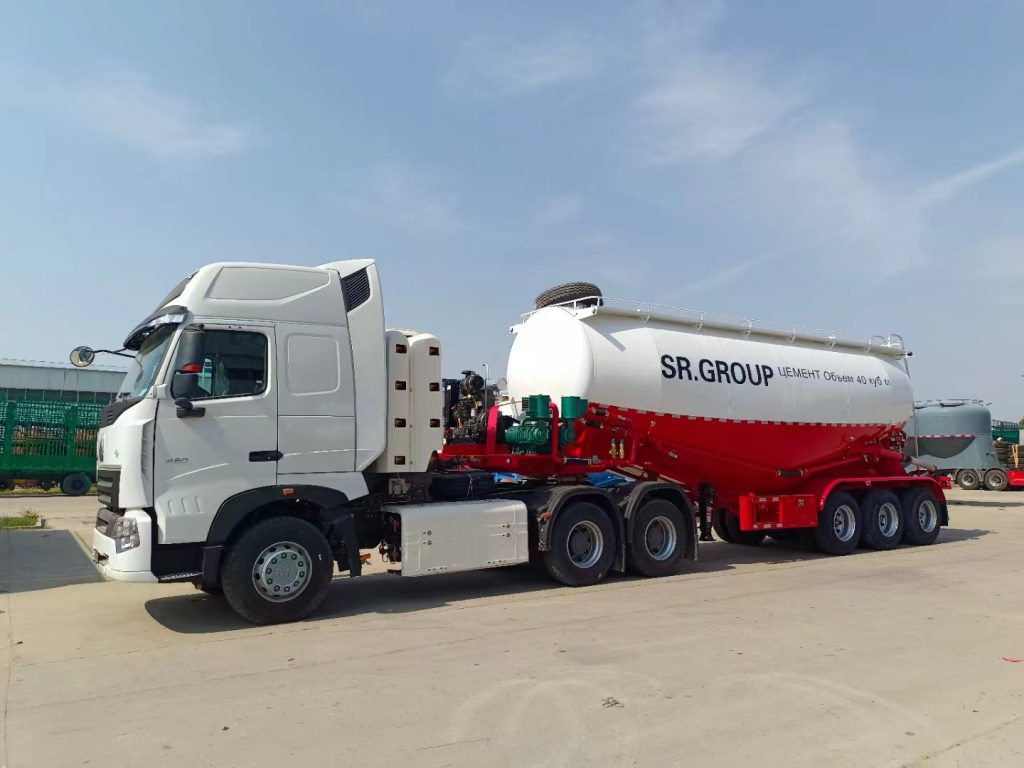
Chemical liquid transport semi-trailer
Chemical liquid transport semi-trailer has different requirements for tank material according to the characteristics of the transported medium.
Commonly used chemical liquid tank materials include: stainless steel (202, 304, 316L), carbon steel, plastic steel (plastic-lined tank), fiberglass, aluminum tank, all-plastic tank (polyethylene, polypropylene), etc. The all-plastic tank series uses polyethylene as the main raw material formulation process, and the overall one-time forming of all-plastic and plastic steel products has the characteristics of seamless, no leakage, corrosion resistance, anti-aging, impact resistance, non-toxicity, long life, and low price. It is suitable for most acids, alkalis, salts, alcohols, aldehydes storage, transportation, reaction, mixing, wastewater, and gas treatment.
Most of them are fixed on the chassis of the car with steel belts as transport tanks. Widely used in chemical, metallurgical, environmental protection, brewing, food, pharmaceutical, storage and transportation and other enterprises. The all-plastic tank series uses polypropylene as the main raw material process. The 20MM thick polypropylene sheet is welded by a special double-sided process. The middle of the tank body is reinforced with multiple wave-breaking plates. It is better than polyethylene tanks (<60℃) in high temperature resistance (polypropylene <85℃). Plastic-steel composite tank series (plastic-lined tank): Steel-plastic composite anti-corrosion series products are modified PE formed integrally on the inner wall of the steel tank through a steel mesh transition structure. They have the dual characteristics of PE anti-corrosion performance and metal strength. The use temperature is -20℃~70℃. The products include pressure tanks, large storage tanks, reactors, ion exchange columns, chemical towers, pipeline valves, etc., which are widely used in storage, reaction and transportation tanks in the chemical industry.
Carbon steel tank series: The inside and outside are treated with detailed anti-corrosion paint, suitable for the transportation of various non-corrosive chemical liquids. Use temperature: -20℃~60℃, the application range is small (concentrated sulfuric acid with a concentration of >97% can be made of 6-8mm thick carbon steel plates) FRP tanks have a wide range of applications. Due to high brittleness and low toughness, the tank body should not be made larger when used as a transport tank. Aluminum tanks are the best choice for transporting liquid nitric acid. Stainless steel tanks have a wide range of applications, but the cost is higher. Our company has strong technical strength and can design and manufacture products that satisfy users according to user requirements.
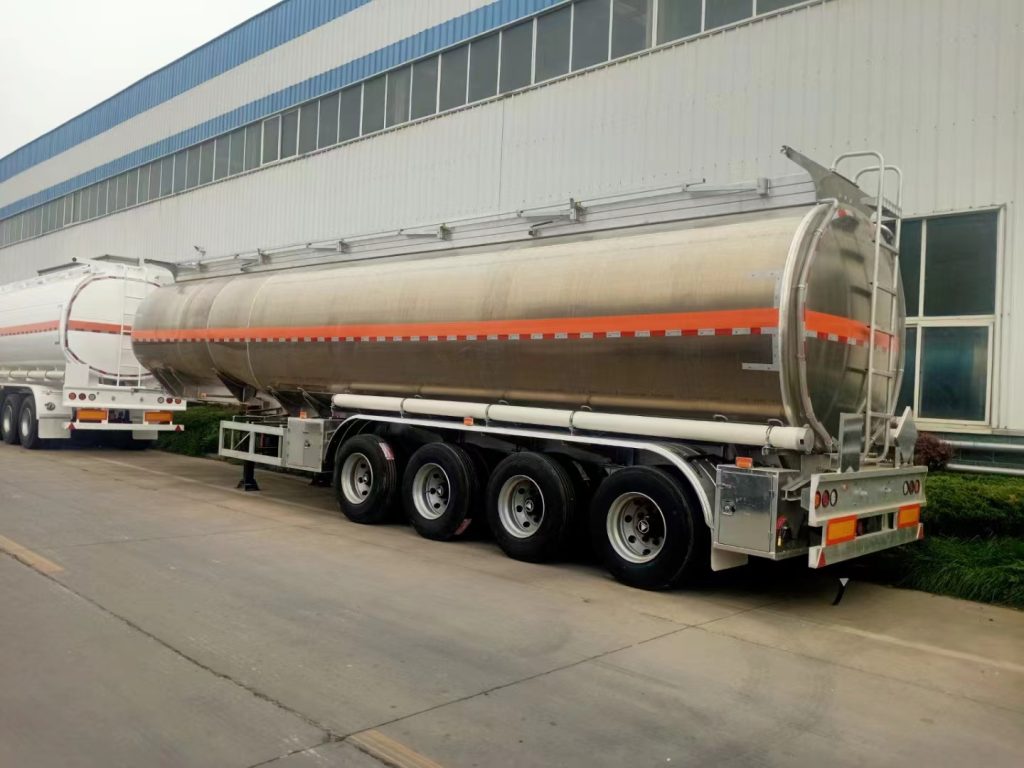